Nickel Chemical Etching
Nickel Etching: A Comprehensive Guide to Precision Manufacturing and Applications
What’s Nickel Etching?
Nickel chemical etching is a specialized process used to create intricate designs and patterns on nickel sheet surfaces. This technique involves the use of chemical solutions to selectively remove material, resulting in precise and detailed components. Nickel etching is widely recognized for its ability to produce high-quality parts.
Hysen has over a decade of extensive experience in nickel etching processing, with mature technology and refined craftsmanship. By nickel etching, we can provide custom and high-precision nickel components, and high-quality nickel etching solutions.
Where’s Nickel Etching used to?
Nickel etching products are widely used across numberous fields due to their versatility and precision. In the electronics industry, nickel etching is used to manufacture high-precision electronic components, such as chip pins and fine circuits on circuit boards. These tiny an precise structures make it possible for electronic products to be miniaturized and have high performance. In addition, in the automotive manufacturing field, nickel etching technology is applied to produce engine fuel injectors, sensor components, etc., improving the precision and durability of automotive parts. Moreover, in the medical device field, the surgical instruments and implants manufactured by nickel etching are of great significance in terms of their fineness and biocompatibility, which are crucial to the treatment effect and health and safety of patients.
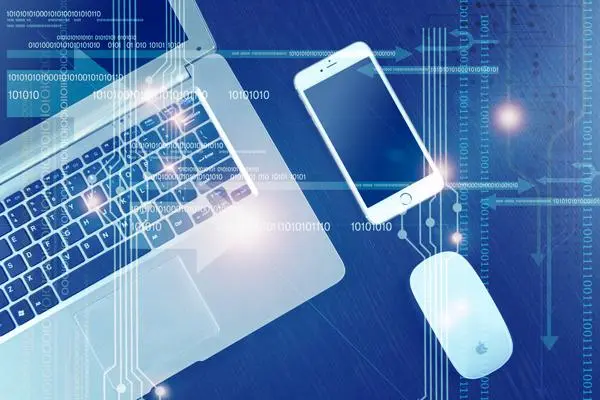
Benefits
Challenges and Considerations
Despite its numberous benefits, nickel etching does present certain challenges. One of the primary difficulties is controlling the etching rate to achieve the desired depth and detail. Moreover, selecting the appropriate chemical solutions is critical to avoid damaging the nickel surface. At the same time, maintaining consistent quality across large batches requires meticulous process control. Additionally, safety followed due to the hazardous nature of the chemicals involved. Lastly, it’s essential to consider the environmental impact of the etching process and implement proper waste management practices.
Our factory has independently developed a unique etching formula, which can effectively solve the industry problems such as precision and surface treatment, ensuring that nickel products meet high-precision standards. Our factory is certified with both the ISO9001 and ISO14001, ensuring that every product meets international standards. We are committed to providing customers with high-precision, high-quality nickel etching solutions while emphasizing environmental protection and sustainable development. Whether for complex designs or large-scale production needs, we can meet customer requirements with efficient and reliable services.
Choose us, you gain a trusted and high-quality partner!