Metal Etching in BMIC (Battery Management Integrated Circuit) Market
Embrace the future of BMIC manufacturing with metal etching – where precision meets performance.
The battery management integrated circuit (BMIC) market is experiencing unprecedented growth, fueled by the demand for advanced energy storage and management systems. At the core of this innovation lies metal etching, a cutting-edge manufacturing process that enables the productiong of high-precision components essential for BMICs. We will delve into it together how metal etching in the BMIC market is driving efficiency, scalability, and performance.
Why Metal Etching is Critical for BMIC Components?
Metal etching is widely used to fabricate key components in both batteries and integrated circuits. In BMICs, it produces lead frames, interconnects, spring connects, and bonding pads, ensuring reliable electrical connections. For batteries, it creates current collectors and electrodes, which are crucial for efficient energy transfer. The ability to achieve micron-level precision makes metal etching indispensable for manufacturing these intricate parts.
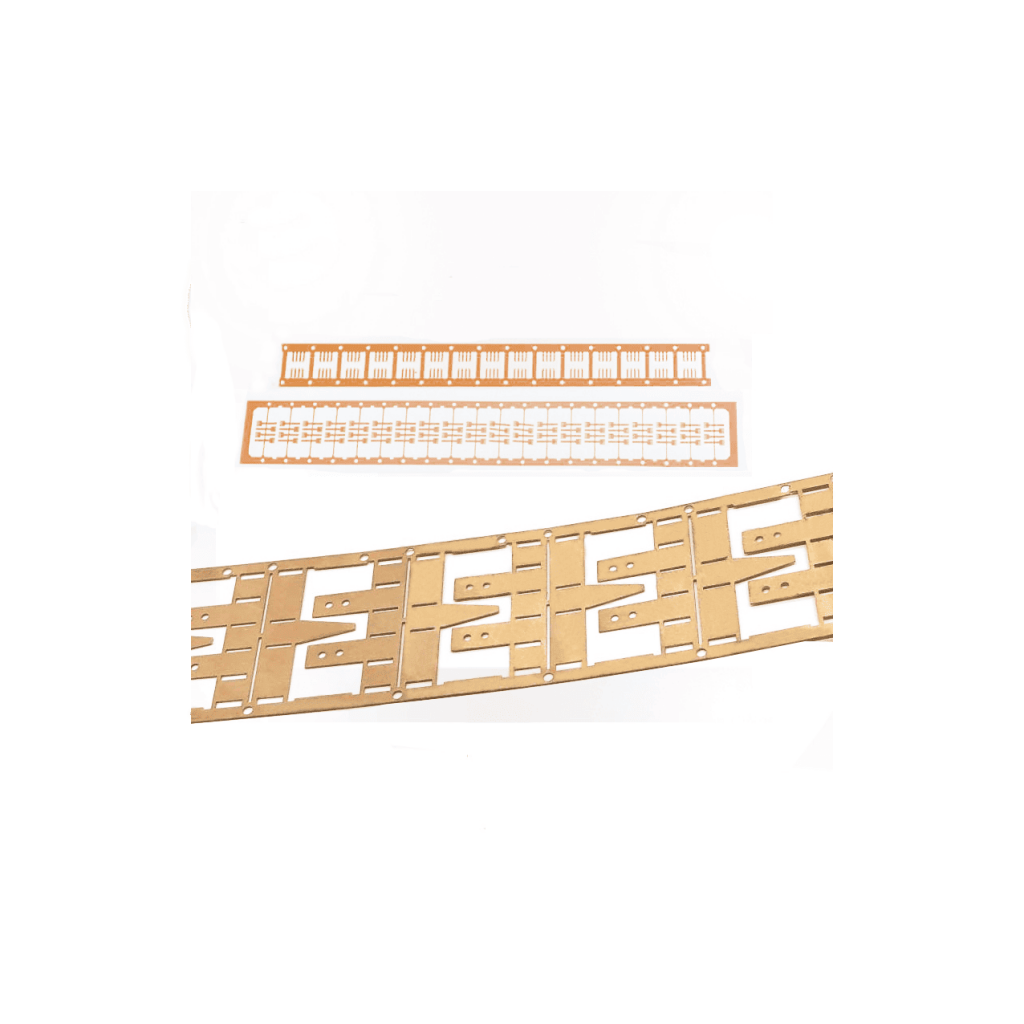
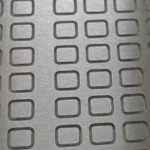
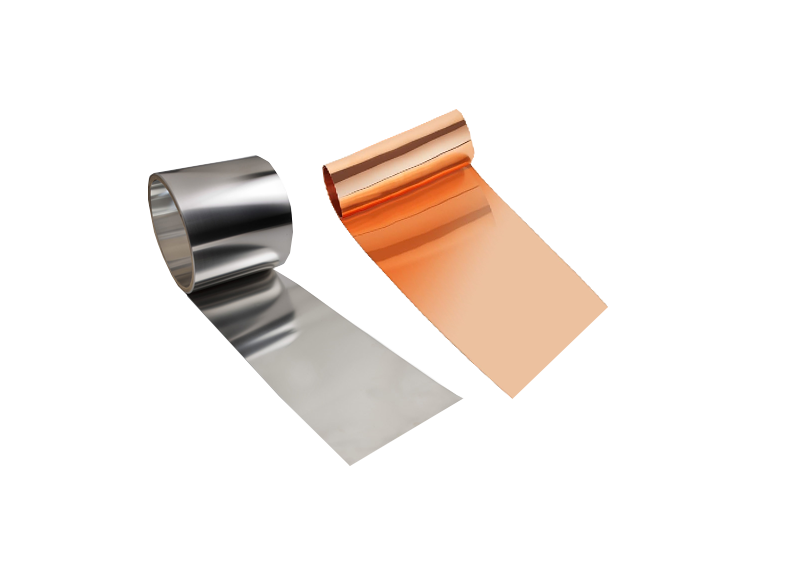
Key Advantages of Metal Etching in BMIC Manufacturing
As the battery management integrated circuit market expands, the need for reliable, high-performance components grows. Metal etching addresses these challenges by offering a cost-effective, scalable, and precise manufacturing solution. Its ability to produce complex, high-quality parts ensures that BMICs can meet the evolving demands of energy storage and management systems.
Metal etching is a game-changer in the BMIC market, enabling the production of components that are both precise and efficient. By leveraging this advanced manufacturing process, Hysen can offer innovative solutions for energy management.